Help Center
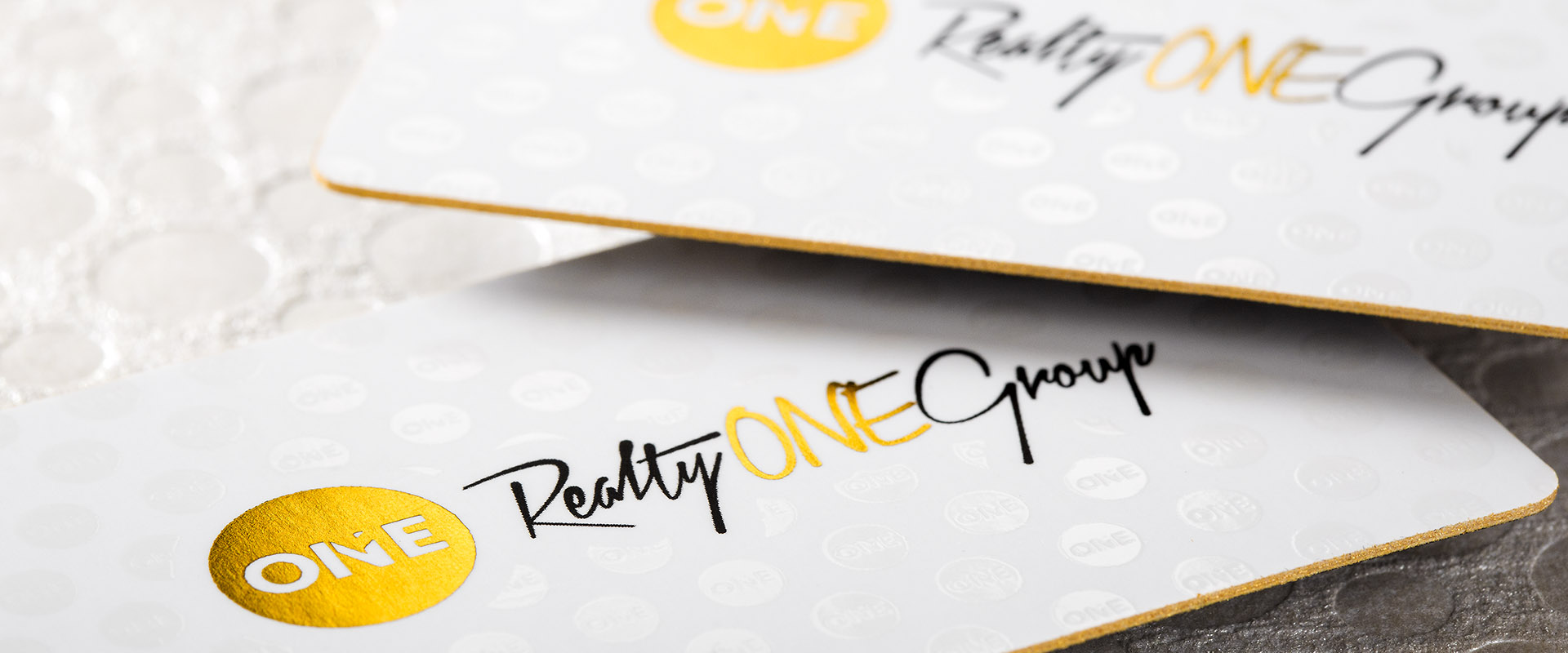
Get Started
We’ve put a lot of time and energy into creating tools for our customers. A Legit Print Account gets you access to instant order tracking, shipping notifications, invoice downloads, order history with reordering, easy custom quotes, and more.
Create an account to start ordering today!
Our product samples are completely free. You’ll have to pay a small fee for postage, but the first order promo inside makes
it all worth it!
Order samples here.
Here’s a quick breakdown.
Bleed -- Always add at least 0.125” bleed to your files. In general, the bigger the product dimensions, the more bleed is encouraged.
Outline Fonts -- Turn all your fonts into smart objects. This will help preserve their appearance.
300dpi Res Images -- Images should be minimum 300dpi resolution for print.
CMYK Color Mode -- We print using CMYK color mode. Make sure your colors are converted.
Printer’s Black -- If your blacks are only 100K, they will come out looking more dark gray than black because you are not utilizing the 4-color process. We recommend 40C 30M 20Y 100K for a true rich black.
Download our size templates here.
How to set up files for Spot UV, Foil, and Embossing.
Can you set up my files for me?
Bleed -- Always add at least 0.125” bleed to your files. In general, the bigger the product dimensions, the more bleed is encouraged.
Outline Fonts -- Turn all your fonts into smart objects. This will help preserve their appearance.
300dpi Res Images -- Images should be minimum 300dpi resolution for print.
CMYK Color Mode -- We print using CMYK color mode. Make sure your colors are converted.
Printer’s Black -- If your blacks are only 100K, they will come out looking more dark gray than black because you are not utilizing the 4-color process. We recommend 40C 30M 20Y 100K for a true rich black.
Your Orders
You can check the most recent status of your order by going to Account > Orders.
We do our best to make sure our system is updated with the most recent status from our production facilities.
Files Received -- We’ve successfully received the files you uploaded and they are waiting to be checked for print-ready status according to our guidelines and templates.
Files Not Received -- We haven’t received any of the necessary files.
Files Partially Received -- We received one or some, but not all of the necessary files.
OK to Print -- Our team has cleared your files for print production.
Imposition -- Your order is being configured and aligned on the print sheet and getting ready for printing.
On press -- Your order is not on the printing press and in production.
Finishing -- Your order is in the last stages of production.
Shipped -- Your order has been assigned a tracking number and has been picked up by shipping carriers. You can access the tracking number by visiting the Order Details section in Your Account.
Files Received -- We’ve successfully received the files you uploaded and they are waiting to be checked for print-ready status according to our guidelines and templates.
Files Not Received -- We haven’t received any of the necessary files.
Files Partially Received -- We received one or some, but not all of the necessary files.
OK to Print -- Our team has cleared your files for print production.
Imposition -- Your order is being configured and aligned on the print sheet and getting ready for printing.
On press -- Your order is not on the printing press and in production.
Finishing -- Your order is in the last stages of production.
Shipped -- Your order has been assigned a tracking number and has been picked up by shipping carriers. You can access the tracking number by visiting the Order Details section in Your Account.
Pay attention! This one’s important if you’re on a deadline.
Turnaround times are estimated, but not guaranteed due to several production variables beyond our control.
We do try our best to stick to the estimated turnaround times, however; we can be late, but we can also be early.
Your Order’s turnaround time begins once our team has cleared your files for print. If there are any issues with your files, they will be
rejected and you will be notified and asked to make corrections. Because of this, it’s important that you follow our Guidelines and Templates
to avoid any delays if you are on a tight deadline.
Here’s an example of a 2-4 Business Day Turnaround: Thursday -- Day 1 (Files received before 11am PST). Friday -- Day 2 of production (earliest ship date).
-- CLOSED WEEKENDS --
Monday -- Day 3 of production. Tuesday -- Day 4 of production (ships same day if finished before 3pm). Wednesday -- Order ships out from the facility.
Our daily production cut-off time is 11am PST. If your files are not approved by this time, your order completion will be shifted by a day.
Here’s an example of a 2-4 Business Day Turnaround: Thursday -- Day 1 (Files received before 11am PST). Friday -- Day 2 of production (earliest ship date).
-- CLOSED WEEKENDS --
Monday -- Day 3 of production. Tuesday -- Day 4 of production (ships same day if finished before 3pm). Wednesday -- Order ships out from the facility.
The easiest, cleanest way to change details of an order is to place another order with the correct specs, then let us know to cancel the original order.
This way, there is no confusion or miscommunication.
If your order has not started production, we will cancel your order and refund your money entirely. No hard feelings. Just be sure to get in touch with us ASAP.
Let us know ASAP! Sometimes shipping carriers arrive to pick up packages ahead of schedule. We have no way of knowing their timing, but once it’s out of our hands; it’s really out of our control.
If you need to change the shipping service speed, or need to reroute a shipment, we will try to assist with that as well. There may be applicable carrier fees depending on what needs to be done.
It’s pretty simple with our new system. Just go to Account > Orders then click the Reorder button beside the order. This will add the same product and specs to your cart.
Fix Problems
File Setup
We accept both vector and raster files, but strongly encourage you to use vector art wherever possible to preserve a crisp appearance. Make sure your fonts are outlined and converted to smart objects, transparencies are flattened, and overprint is turned off. Any raster elements need to be minimum 300dpi resolution.Offset vs. Digital Printing
Most of our products are run on big offset presses, which output a higher quality print but require a higher minimum run. We use digital presses when the minimum quantity is lower (25-250). Digital printing offers great value in print quality, low minimums, and fast turnarounds. However, digital prints use a bunch of tiny dots to make up your artwork. With light colors and thin lines, these dots tend to be more visible. A good rule of thumb is to use vector graphics whenever possible and make sure raster graphics and images are 300dpi resolution, minimum. If you’re not sure whether your order will run digitally or offset, please reach out and ask our team and they’ll be happy to help.
You probably noticed our website isn’t set up for international addresses/users yet. We’re working on that! In the meantime,
please reach out to our team so we can figure out how we can accommodate you!
Printing is usually done using a CMYK color process. This offers the ability to create an infinite amount of colors, but also limits the ability to
be 100% accurate all the time. We do try our best to stay true to the intended colors. We recommend creating and viewing all graphics in CMYK color
mode, and checking them on multiple screens for the best results.
If your project demands color precision, please reach out to us about custom Pantone colors for your project.
Your computer screen outputs colors in RGB and has a light source to illuminate graphics. Printing is done using CMYK and uses the brightness of the
paper to mimic the light source. Because of this, printing will always come out darker than what you see on screen.
The total value of your CMYK values added together is called your Ink Coverage. Generally, the higher the overall Ink Coverage is; the darker your print
will be. Think of it this way: ink is water-based and translucent, so the more ink you are applying, the less the brightness of the white paper shows
through; making your prints darker.
We suggest a total Ink Coverage of 280% or less on any given color.
The most common reason for payment issues is incorrect information. Please double and triple-check your card number, cardholder name, expiration date,
security code, and especially the billing address.
An incorrect billing address is often the reason payments don’t go through. We suggest checking your most recent credit card billing statement to make
sure you have the most up-to-date address.
Product Info
We’ve got more options than froyo toppings, but we organized them nice and neatly for you in this glossary.
We understand your needs for wanting to make sure things meet your expectations before printing an entire bulk order. Unfortunately, because our
products are often customized with special finishes like Spot UV, Foil, Pantone inks, etc, we cannot offer one-off test prints.
However, if you have a larger order, and want to print the minimum quantity as a test print, we can absolutely do that for you!
Breath! This is easier than you think.
Decide what parts of your design you want to apply the special finish to. Turn off all the other layers, or just remove them. You
should just be left with objects that will have the special finish. Select the objects and make them 100% Black (0C 0M 0Y 100K).
This is your mask file.
Make sure you remove the special finish objects from your regular print file! Having the objects in both print and mask files will
cause problems in printing.
Of course! A lot of our customers are creative professionals who love to own the creative process, but we understand that’s
not everyone. Whether you just have an idea, or you already have a logo and brand style guide; we have design services for
any scenario.
Your Account
If you’re having trouble signing into your account, try resetting your password.
If you still have issues, please contact our team.